'75 Bus Ignition Wiring Question
- tractoman
- Getting Hooked!
- Location: Sonoma, CA
- Status: Offline
'75 Bus Ignition Wiring Question
While attempting to repair my leaky washer hoses at the valve in the steering column, and during removal of the turn signal switch plugs, the wires come flying off the ignition switch. I was able to get the ignition switch all plugged back in correctly, one wire at a time thanks to the Bentley, and then it hits me, shouldn't there be a plug on the end of these wires that plug into the ignition switch? Is there a source for a new one assuming there should be one or do I need a donor?
Thanks,
Mike
'75 Westy
Mike
'75 Westy
- KYLE
- I'm New!
- Location: Elyria, OH
- Contact:
- Status: Offline
- Amskeptic
- IAC "Help Desk"
- Status: Offline
I have a dumbass hack method of wire splicing in tight confines, particularly with high amperage requirements. I do not like crimp connectors.
Splice your big wires back at least 3/4" . Slip a 1 1/2" piece of heat shrink over one of them. Mate the two spliced wires at the midpoint of each splice-back and twist the two together such that the end of each is lined up at the insulation of the other. Wind tightly. Get out the soldering gun and heat the midpoint of the exposed strand and put your rosin-core solder end on the other side. The instant that the solder flows release the soldering gun. Slide the heat shrink over the exposed tinned strands, and apply your Bic lighter to the heat shrink.
This method will allow you to run your wiring/harnesses through the stock tie down points and it will be more than up to any current demands.
Colin
Splice your big wires back at least 3/4" . Slip a 1 1/2" piece of heat shrink over one of them. Mate the two spliced wires at the midpoint of each splice-back and twist the two together such that the end of each is lined up at the insulation of the other. Wind tightly. Get out the soldering gun and heat the midpoint of the exposed strand and put your rosin-core solder end on the other side. The instant that the solder flows release the soldering gun. Slide the heat shrink over the exposed tinned strands, and apply your Bic lighter to the heat shrink.
This method will allow you to run your wiring/harnesses through the stock tie down points and it will be more than up to any current demands.
Colin
BobD - 78 Bus . . . 112,730 miles
Chloe - 70 bus . . . 217,593 miles
Naranja - 77 Westy . . . 142,970 miles
Pluck - 1973 Squareback . . . . . . 55,600 miles
Alexus - 91 Lexus LS400 . . . 96,675 miles
Chloe - 70 bus . . . 217,593 miles
Naranja - 77 Westy . . . 142,970 miles
Pluck - 1973 Squareback . . . . . . 55,600 miles
Alexus - 91 Lexus LS400 . . . 96,675 miles
- KYLE
- I'm New!
- Location: Elyria, OH
- Contact:
- Status: Offline
I like to do everything just as you described, but I also crimp the splice together with a splice clip.
It is still recommended to solder the connection, but I have found it faster to just make a secure crimp as opposed to twisting the wires together. Sometimes I am doing this up to 100 times a day and it saves my finger tips too.
I also make sure and use the adhesive lined shrink tube. It has a flowable inner layer that creates a sealed splice and avoids corrosion.
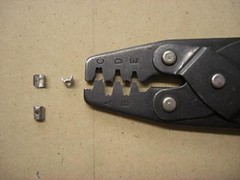

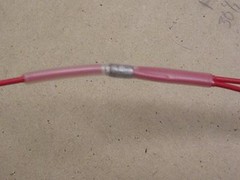
It is still recommended to solder the connection, but I have found it faster to just make a secure crimp as opposed to twisting the wires together. Sometimes I am doing this up to 100 times a day and it saves my finger tips too.
I also make sure and use the adhesive lined shrink tube. It has a flowable inner layer that creates a sealed splice and avoids corrosion.
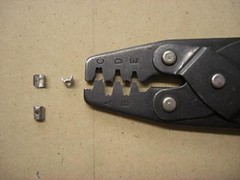

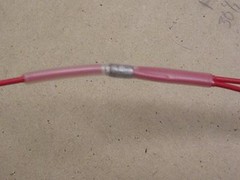